chapter 8-9
DownloadTélécharger
Actions
Vote :
ScreenshotAperçu
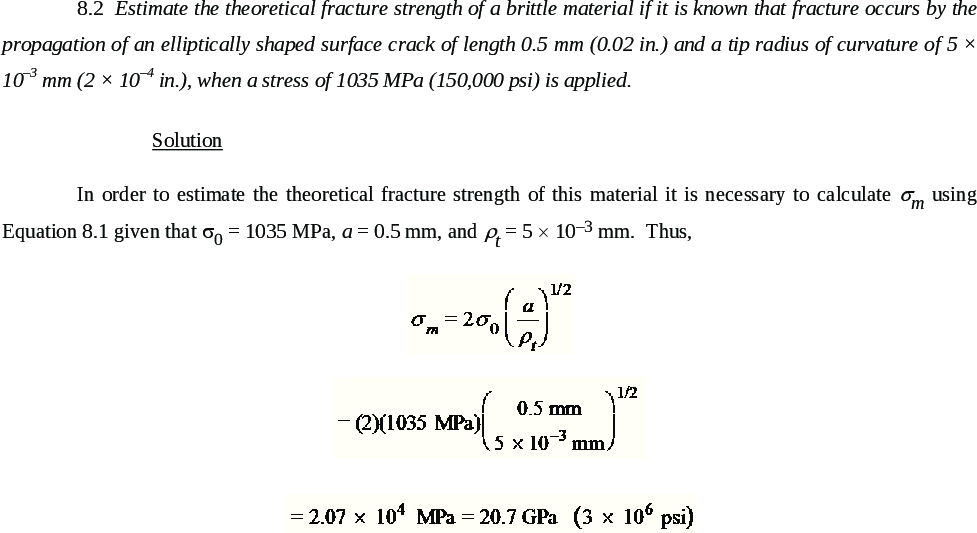
Informations
Catégorie :Category: mViewer GX Creator Lua TI-Nspire
Auteur Author: didierisaza
Type : Classeur 3.6
Page(s) : 15
Taille Size: 720.40 Ko KB
Mis en ligne Uploaded: 30/04/2015 - 09:18:05
Uploadeur Uploader: carl cox (Profil)
Téléchargements Downloads: 162
Visibilité Visibility: Archive publique
Shortlink : https://tipla.net/a205965
Type : Classeur 3.6
Page(s) : 15
Taille Size: 720.40 Ko KB
Mis en ligne Uploaded: 30/04/2015 - 09:18:05
Uploadeur Uploader: carl cox (Profil)
Téléchargements Downloads: 162
Visibilité Visibility: Archive publique
Shortlink : https://tipla.net/a205965
Description
8.2 Estimate the theoretical fracture strength of a brittle material if it is known that fracture occurs by the
propagation of an elliptically shaped surface crack of length 0.5 mm (0.02 in.) and a tip radius of curvature of 5 ×
10–3 mm (2 × 10–4 in.), when a stress of 1035 MPa (150,000 psi) is applied.
Solution
In order to estimate the theoretical fracture strength of this material it is necessary to calculate Vm using
Equation 8.1 given that V0 = 1035 MPa, a = 0.5 mm, and Ut = 5 u 103 mm. Thus,
8.4 An MgO component must not fail when a tensile stress of 13.5 MPa (1960 psi) is applied. Determine
the maximum allowable surface crack length if the surface energy of MgO is 1.0 J/m2. Data found in Table 12.5 may
prove helpful.
Solution
The maximum allowable surface crack length for MgO may be determined using a rearranged form of
Equation 8.3. Taking 225 GPa as the modulus of elasticity (Table 12.5), and realizing that values of Vc (13.5 MPa)
and Js (1.0 J/m2) are given in the problem statement, we solve for a, as follows:
8.6 An aircraft component is fabricated from an aluminum alloy that has a plane strain fracture toughness
of 40 MPa (36.4 ksi ). It has been determined that fracture results at a stress of 300 MPa (43,500 psi) when
the maximum (or critical) internal crack length is 4.0 mm (0.16 in.). For this same component and alloy, will
fracture occur at a stress level of 260 MPa (38,000 psi) when the maximum internal crack length is 6.0 mm (0.24
in.)? Why or why not?
Solution
We are asked to determine if an aircraft component will fracture for a given fracture toughness (40
), stress level (260 MPa), and maximum internal crack length (6.0 mm), given that fracture occurs for the
same component using the same alloy for another stress level and internal crack length. (Note: Because the cracks
are internal, their lengths are equal to 2a.) It first becomes necessary to solve for the parameter Y, using Equation
8.5, for the conditions under which fracture occurred (i.e., V = 300 MPa and 2a = 4.0 mm). Therefore,
Now we will solve for the product for the other set of conditions, so as to ascertain whether or not this
value is greater than the KIc for the alloy. Thus,
Therefore, fracture will occur since this value is greater than the KIc of the material, .
8.10 Calculate the maximum internal crack length allowable for a Ti-6Al-4V titanium alloy (Table 8.1)
component that is loaded to a stress one-half its yield strength. Assume that the value of Y is 1.50.
Solution
This problem asks us to calculate the maximum internal crack length allowable for the Ti-6Al-4V titanium
alloy in Table 8.1 given that it is loaded to a stress level equal to one-half of its yield strength. For this alloy,
; also, V = Vy/2 = (910 MPa)/2 = 455 MPa. Now solving for 2ac (since this crack is an internal
one) using Equation 8.7 yields
8.11 A structural component in the form of a wide plate is to be fabricated from a steel alloy that has a
plane-strain fracture toughness of ( ) and a yield strength of 860 MPa (125,000 psi). The
flaw size resolution limit of the flaw detection apparatus is 3.0 mm (0.12 in.). If the design stress is one-half the yield
strength and the value of Y is 1.0, determine whether a critical flaw for this plate is subject to detection.
Solution
This problem asks that we determine whether or not a critical flaw in a wide plate is subject to detection
given the limit of the flaw detection apparatus (3.0 mm), the value of KIc , the design stress (Vy/2
in which Vy = 860 MPa), and Y = 1.0. We first need to compute the value of ac using Equation 8.7; thus
Therefore, the critical flaw is subject to detection since this value of ac (16.8 mm) is greater than the 3.0 mm
resolution limit.
8.12 After consultation of other references, write a brief report on one or two nondestructive test
techniques that are used to detect and measure internal and/or surface flaws in metal alloys.
The student should answer this question on his/her own.
Crack Initiation and Propagation
Factors That Affect Fatigue Life
8.28 Briefly explain the difference between fatigue striations and beachmarks in terms of (a) size and (b)
origin.
Solution
(a) With regard to size, beachmarks are normally of macroscopic dimensions and may be observed with
the naked eye; fatigue striations are of microscopic size and it is necessary to observe them using electron
microscopy.
(b) With regard to origin, beachmarks result from interruptions in the stress cycles; each fatigue striation is
corresponds to the advance of a fatigue crack during a single load cycle.
8.40 (a) Estimate the activation energy for creep (i.e., Qc in Equation 8.25) for the S-590 alloy having the
steady-state creep behavior shown in Figure 8.32. Use data taken at a stress level of 300 MPa (43,500 psi) and
temperatures of 650qC and 730qC. Assume that the stress exponent n is independent of temperature.
(b) Estimate at 600qC (873 K) and 300 MPa.
Solution
(a) We are asked to estimate the activation energy for creep for the S-590 alloy having the steady-state
creep behavior shown in Figure 8.32, using data taken at V = 300 MPa (43,500 psi) and temperatures of 650qC and
730qC. Since V is a constant, Equation 8.25 takes the form
(8.25a)
where is now a constant (since V and n are now constants) . (Note: the exponent n has about the same value at
these two temperatures per Problem 8.39.) Taking natural logarithms of the above expression
For the case in which we have creep data at two temperatures (denoted as T1 and T2) and their corresponding steady-
state creep rates ( and ), it is possible to set up two simultaneous equations of the form as above, with two
unknowns, namely and Qc. Solving for the above equation for Qc yields
Let us choose T1 as 650qC (923 K) and T2 as 730qC (1003 K); then from Figure 8.32, at V = 300 MPa, = 104
h1 and = 102 h1. Substitution of these values into the above equation leads to
= 442,800 J/mol
(b) We are now asked to estimate at 600qC (873 K). It is first necessary to determine the value of ,
which is accomplished Equation 8.25a, the value of Qc, and one of the two values and its temperature T (say
and T1). Thus,
Now it is possible to calculate at 600qC (873 K) as follows:
Interpretation of Phase Diagrams
9.10 Cite the phases that are present and the phase compositions for the following alloys:
(a) 15 wt% Sn–85 wt% Pb at 100°C (212°F)
(b) 25 wt% Pb–75 wt% Mg at 425°C (800°F)
(c) 85 wt% Ag–15 wt% Cu at 800°C (1470°F)
(d) 55 wt% Zn–45 wt% Cu at 600°C (1110°F)
(e) 1.25 kg Sn and 14 kg Pb at 200°C (390°F)
(f) 7.6 lbm Cu and 144.4 lbm Zn at 600°C (1110°F)
(g) 21.7 mol Mg and 35.4 mol Pb at 350°C (660°F)
(h) 4.2 mol Cu and 1.1 mol Ag at 900°C (1650°F)
Solution
(a) For an alloy composed of 15 wt% Sn-85 wt% Pb and at 100qC, from Figure 9.8, D and E phases are
present, and using a tie line constructed at this temperature, the compositions of these phases are determined as
follows:
CD = 5 wt% Sn-95 wt% Pb
CE = 98 wt% Sn-2 wt% Pb
(b) For an alloy composed of 25 wt% Pb-75 wt% Mg and at 425qC, from Figure 9.20, only the D phase is
present; its composition is 25 wt% Pb-75 wt% Mg.
(c) For an alloy composed of 85 wt% Ag-15 wt% Cu and at 800qC, from Figure 9.7, E and liquid phases
are present, and using a tie line constructed at this temperature the compositions of these phases are determined as
follows:and
CE = 92 wt% Ag-8 wt% Cu
CL = 77 wt% Ag-23 wt% Cu
(d) For an alloy composed of 55 wt% Zn-45 wt% Cu and at 600qC, from Figure 9.19, E and J phases are
present, and using a tie line constructed at this temperature, the compositions of these phases are determined as
follows:and
CE = 51 wt% Zn-49 wt% Cu
CJ = 58 wt% Zn-42 wt% Cu
(e) For an alloy composed of 1.25 kg Sn and 14 kg Pb and at 200qC, we must first determine the Sn and Pb
concentrations in weight percent (using Equation 4.3a), as
From Figure 9.8, only the D phase is present; its composition is 8.2 wt% Sn-91.8 wt% Pb.
(f) For an alloy composed of 7.6 lbm Cu and 144.4 lbm Zn and at 600qC, we must first determine the Cu
and Zn concentrations (using Equation 4.3a), as
Formatted: Line spacing: single
From Figure 9.19, only the L phase is present; its composition is 95.0 wt% Zn-5.0 wt% Cu
(g) For an alloy composed of 21.7 mol Mg and 35.4 mol Pb and at 350qC, it is necessary to determine the
Mg and Pb concentrations in weight percent. However, we must first compute the masses of Mg and Pb (in grams)
using a rearranged form of Equation 4.4 (and the atomic weights of Pb and Mg—207.2 g/mol and 24.31 g/mol) as
follows:
Now, using Equation 4.3a, concentrations of Pb and Mg are determined as follows:
9.14 A 50 wt% Ni–50 wt% Cu alloy is slowly cooled from 1400°C (2550°F) to 1200°C (2190°F).
(a) At what temperature does the first solid phase form?
(b) What is the composition of this solid phase?
(c) At what temperature does the liquid solidify?
(d) What is the composition of this last remaining liquid phase?
Solution
Shown below is the Cu-Ni phase diagram (Figure 10.3a) and a vertical line constructed at a composition of
50 wt% Ni-50 wt% Cu.
(a) The first solid phase forms at the temperature at which a vertical line at this composition intersects the
L–(D + L) phase boundary--i.e., at about 1320qC.
(b) The composition of this solid phase corresponds to the intersection with the L–(D + L) phase boundary,
of a tie line constructed across the D + L phase region at 1320qC--i.e., CD = 62 wt% Ni-38 wt% Cu.
(c) Complete solidification of the alloy occurs at the intersection of this same vertical line at 50 wt% Ni
with the (D+ L)–D phase boundary--i.e., at about 1270qC.
(d) The composition of the last liquid phase remaining prior to complete solidification corresponds to the
intersection with the L–(D+ L) boundary, of the tie line constructed across the D+ L phase region at 1270qC--i.e.,
CL is about 37 wt% Ni-63 wt% Cu.
9.21 A 65 wt% Ni–35 wt&XDOORLVKHDWHGWRDWHPSHUDWXUHZLWKLQWKHͣOLTXLG-phase region. If the
FRPSRVLWLRQRIWKHͣSKDVHLVZW1LGHWHUPLQH
(a) The temperature of the alloy
(b) The composition of the liquid phase
(c) The mass fractions of both phases
Solution
(a) In order to determine the temperature of a 65 wt% Ni-35 wt% Cu alloy for which D and liquid phases
are present with theD phase of composition 70 wt% Ni, we need to construct a tie line across the D + L phase region
of Figure 10.3a that intersects the solidus line at 70 wt% Ni; this is possible at about 1345qC.
(b) The composition of the liquid phase at this temperature is determined from the intersection of this same
tie line with liquidus line, which corresponds to about 59 wt% Ni.
(c) The mass fractions of the two phases are determined using the lever rule, Equations 9.1 and 9.2 with C0
= 65 wt% Ni, CL = 59 wt% Ni, and CD = 70 wt% Ni, as
9.43 For a 76 wt% Pb–24 wt% Mg alloy, make schematic sketches of the microstructure that would be
observed for conditions of very slow cooling at the following temperatures: 575°C (1070°F), 500°C (930°F), 450°C
(840°F), and 300°C (570°F). Label all phases and indicate their approximate compositions.
Solution
The illustration below is the Mg-Pb phase diagram (Figure 9.20). A vertical line at a composition of 76
wt% Pb-24 wt% Mg has been drawn, and, in addition, horizontal arrows at the four temperatures called for in the
problem statement (i.e., 575qC, 500qC, 450qC, and 300qC).
Formatted: Font: Liberation Serif
On the basis of the locations of the four temperature-composition points, schematic sketches of the four respective
microstructures along with phase compositions are epresented as follows:
Formatted: Font: Liberation Serif
propagation of an elliptically shaped surface crack of length 0.5 mm (0.02 in.) and a tip radius of curvature of 5 ×
10–3 mm (2 × 10–4 in.), when a stress of 1035 MPa (150,000 psi) is applied.
Solution
In order to estimate the theoretical fracture strength of this material it is necessary to calculate Vm using
Equation 8.1 given that V0 = 1035 MPa, a = 0.5 mm, and Ut = 5 u 103 mm. Thus,
8.4 An MgO component must not fail when a tensile stress of 13.5 MPa (1960 psi) is applied. Determine
the maximum allowable surface crack length if the surface energy of MgO is 1.0 J/m2. Data found in Table 12.5 may
prove helpful.
Solution
The maximum allowable surface crack length for MgO may be determined using a rearranged form of
Equation 8.3. Taking 225 GPa as the modulus of elasticity (Table 12.5), and realizing that values of Vc (13.5 MPa)
and Js (1.0 J/m2) are given in the problem statement, we solve for a, as follows:
8.6 An aircraft component is fabricated from an aluminum alloy that has a plane strain fracture toughness
of 40 MPa (36.4 ksi ). It has been determined that fracture results at a stress of 300 MPa (43,500 psi) when
the maximum (or critical) internal crack length is 4.0 mm (0.16 in.). For this same component and alloy, will
fracture occur at a stress level of 260 MPa (38,000 psi) when the maximum internal crack length is 6.0 mm (0.24
in.)? Why or why not?
Solution
We are asked to determine if an aircraft component will fracture for a given fracture toughness (40
), stress level (260 MPa), and maximum internal crack length (6.0 mm), given that fracture occurs for the
same component using the same alloy for another stress level and internal crack length. (Note: Because the cracks
are internal, their lengths are equal to 2a.) It first becomes necessary to solve for the parameter Y, using Equation
8.5, for the conditions under which fracture occurred (i.e., V = 300 MPa and 2a = 4.0 mm). Therefore,
Now we will solve for the product for the other set of conditions, so as to ascertain whether or not this
value is greater than the KIc for the alloy. Thus,
Therefore, fracture will occur since this value is greater than the KIc of the material, .
8.10 Calculate the maximum internal crack length allowable for a Ti-6Al-4V titanium alloy (Table 8.1)
component that is loaded to a stress one-half its yield strength. Assume that the value of Y is 1.50.
Solution
This problem asks us to calculate the maximum internal crack length allowable for the Ti-6Al-4V titanium
alloy in Table 8.1 given that it is loaded to a stress level equal to one-half of its yield strength. For this alloy,
; also, V = Vy/2 = (910 MPa)/2 = 455 MPa. Now solving for 2ac (since this crack is an internal
one) using Equation 8.7 yields
8.11 A structural component in the form of a wide plate is to be fabricated from a steel alloy that has a
plane-strain fracture toughness of ( ) and a yield strength of 860 MPa (125,000 psi). The
flaw size resolution limit of the flaw detection apparatus is 3.0 mm (0.12 in.). If the design stress is one-half the yield
strength and the value of Y is 1.0, determine whether a critical flaw for this plate is subject to detection.
Solution
This problem asks that we determine whether or not a critical flaw in a wide plate is subject to detection
given the limit of the flaw detection apparatus (3.0 mm), the value of KIc , the design stress (Vy/2
in which Vy = 860 MPa), and Y = 1.0. We first need to compute the value of ac using Equation 8.7; thus
Therefore, the critical flaw is subject to detection since this value of ac (16.8 mm) is greater than the 3.0 mm
resolution limit.
8.12 After consultation of other references, write a brief report on one or two nondestructive test
techniques that are used to detect and measure internal and/or surface flaws in metal alloys.
The student should answer this question on his/her own.
Crack Initiation and Propagation
Factors That Affect Fatigue Life
8.28 Briefly explain the difference between fatigue striations and beachmarks in terms of (a) size and (b)
origin.
Solution
(a) With regard to size, beachmarks are normally of macroscopic dimensions and may be observed with
the naked eye; fatigue striations are of microscopic size and it is necessary to observe them using electron
microscopy.
(b) With regard to origin, beachmarks result from interruptions in the stress cycles; each fatigue striation is
corresponds to the advance of a fatigue crack during a single load cycle.
8.40 (a) Estimate the activation energy for creep (i.e., Qc in Equation 8.25) for the S-590 alloy having the
steady-state creep behavior shown in Figure 8.32. Use data taken at a stress level of 300 MPa (43,500 psi) and
temperatures of 650qC and 730qC. Assume that the stress exponent n is independent of temperature.
(b) Estimate at 600qC (873 K) and 300 MPa.
Solution
(a) We are asked to estimate the activation energy for creep for the S-590 alloy having the steady-state
creep behavior shown in Figure 8.32, using data taken at V = 300 MPa (43,500 psi) and temperatures of 650qC and
730qC. Since V is a constant, Equation 8.25 takes the form
(8.25a)
where is now a constant (since V and n are now constants) . (Note: the exponent n has about the same value at
these two temperatures per Problem 8.39.) Taking natural logarithms of the above expression
For the case in which we have creep data at two temperatures (denoted as T1 and T2) and their corresponding steady-
state creep rates ( and ), it is possible to set up two simultaneous equations of the form as above, with two
unknowns, namely and Qc. Solving for the above equation for Qc yields
Let us choose T1 as 650qC (923 K) and T2 as 730qC (1003 K); then from Figure 8.32, at V = 300 MPa, = 104
h1 and = 102 h1. Substitution of these values into the above equation leads to
= 442,800 J/mol
(b) We are now asked to estimate at 600qC (873 K). It is first necessary to determine the value of ,
which is accomplished Equation 8.25a, the value of Qc, and one of the two values and its temperature T (say
and T1). Thus,
Now it is possible to calculate at 600qC (873 K) as follows:
Interpretation of Phase Diagrams
9.10 Cite the phases that are present and the phase compositions for the following alloys:
(a) 15 wt% Sn–85 wt% Pb at 100°C (212°F)
(b) 25 wt% Pb–75 wt% Mg at 425°C (800°F)
(c) 85 wt% Ag–15 wt% Cu at 800°C (1470°F)
(d) 55 wt% Zn–45 wt% Cu at 600°C (1110°F)
(e) 1.25 kg Sn and 14 kg Pb at 200°C (390°F)
(f) 7.6 lbm Cu and 144.4 lbm Zn at 600°C (1110°F)
(g) 21.7 mol Mg and 35.4 mol Pb at 350°C (660°F)
(h) 4.2 mol Cu and 1.1 mol Ag at 900°C (1650°F)
Solution
(a) For an alloy composed of 15 wt% Sn-85 wt% Pb and at 100qC, from Figure 9.8, D and E phases are
present, and using a tie line constructed at this temperature, the compositions of these phases are determined as
follows:
CD = 5 wt% Sn-95 wt% Pb
CE = 98 wt% Sn-2 wt% Pb
(b) For an alloy composed of 25 wt% Pb-75 wt% Mg and at 425qC, from Figure 9.20, only the D phase is
present; its composition is 25 wt% Pb-75 wt% Mg.
(c) For an alloy composed of 85 wt% Ag-15 wt% Cu and at 800qC, from Figure 9.7, E and liquid phases
are present, and using a tie line constructed at this temperature the compositions of these phases are determined as
follows:and
CE = 92 wt% Ag-8 wt% Cu
CL = 77 wt% Ag-23 wt% Cu
(d) For an alloy composed of 55 wt% Zn-45 wt% Cu and at 600qC, from Figure 9.19, E and J phases are
present, and using a tie line constructed at this temperature, the compositions of these phases are determined as
follows:and
CE = 51 wt% Zn-49 wt% Cu
CJ = 58 wt% Zn-42 wt% Cu
(e) For an alloy composed of 1.25 kg Sn and 14 kg Pb and at 200qC, we must first determine the Sn and Pb
concentrations in weight percent (using Equation 4.3a), as
From Figure 9.8, only the D phase is present; its composition is 8.2 wt% Sn-91.8 wt% Pb.
(f) For an alloy composed of 7.6 lbm Cu and 144.4 lbm Zn and at 600qC, we must first determine the Cu
and Zn concentrations (using Equation 4.3a), as
Formatted: Line spacing: single
From Figure 9.19, only the L phase is present; its composition is 95.0 wt% Zn-5.0 wt% Cu
(g) For an alloy composed of 21.7 mol Mg and 35.4 mol Pb and at 350qC, it is necessary to determine the
Mg and Pb concentrations in weight percent. However, we must first compute the masses of Mg and Pb (in grams)
using a rearranged form of Equation 4.4 (and the atomic weights of Pb and Mg—207.2 g/mol and 24.31 g/mol) as
follows:
Now, using Equation 4.3a, concentrations of Pb and Mg are determined as follows:
9.14 A 50 wt% Ni–50 wt% Cu alloy is slowly cooled from 1400°C (2550°F) to 1200°C (2190°F).
(a) At what temperature does the first solid phase form?
(b) What is the composition of this solid phase?
(c) At what temperature does the liquid solidify?
(d) What is the composition of this last remaining liquid phase?
Solution
Shown below is the Cu-Ni phase diagram (Figure 10.3a) and a vertical line constructed at a composition of
50 wt% Ni-50 wt% Cu.
(a) The first solid phase forms at the temperature at which a vertical line at this composition intersects the
L–(D + L) phase boundary--i.e., at about 1320qC.
(b) The composition of this solid phase corresponds to the intersection with the L–(D + L) phase boundary,
of a tie line constructed across the D + L phase region at 1320qC--i.e., CD = 62 wt% Ni-38 wt% Cu.
(c) Complete solidification of the alloy occurs at the intersection of this same vertical line at 50 wt% Ni
with the (D+ L)–D phase boundary--i.e., at about 1270qC.
(d) The composition of the last liquid phase remaining prior to complete solidification corresponds to the
intersection with the L–(D+ L) boundary, of the tie line constructed across the D+ L phase region at 1270qC--i.e.,
CL is about 37 wt% Ni-63 wt% Cu.
9.21 A 65 wt% Ni–35 wt&XDOORLVKHDWHGWRDWHPSHUDWXUHZLWKLQWKHͣOLTXLG-phase region. If the
FRPSRVLWLRQRIWKHͣSKDVHLVZW1LGHWHUPLQH
(a) The temperature of the alloy
(b) The composition of the liquid phase
(c) The mass fractions of both phases
Solution
(a) In order to determine the temperature of a 65 wt% Ni-35 wt% Cu alloy for which D and liquid phases
are present with theD phase of composition 70 wt% Ni, we need to construct a tie line across the D + L phase region
of Figure 10.3a that intersects the solidus line at 70 wt% Ni; this is possible at about 1345qC.
(b) The composition of the liquid phase at this temperature is determined from the intersection of this same
tie line with liquidus line, which corresponds to about 59 wt% Ni.
(c) The mass fractions of the two phases are determined using the lever rule, Equations 9.1 and 9.2 with C0
= 65 wt% Ni, CL = 59 wt% Ni, and CD = 70 wt% Ni, as
9.43 For a 76 wt% Pb–24 wt% Mg alloy, make schematic sketches of the microstructure that would be
observed for conditions of very slow cooling at the following temperatures: 575°C (1070°F), 500°C (930°F), 450°C
(840°F), and 300°C (570°F). Label all phases and indicate their approximate compositions.
Solution
The illustration below is the Mg-Pb phase diagram (Figure 9.20). A vertical line at a composition of 76
wt% Pb-24 wt% Mg has been drawn, and, in addition, horizontal arrows at the four temperatures called for in the
problem statement (i.e., 575qC, 500qC, 450qC, and 300qC).
Formatted: Font: Liberation Serif
On the basis of the locations of the four temperature-composition points, schematic sketches of the four respective
microstructures along with phase compositions are epresented as follows:
Formatted: Font: Liberation Serif