chapter6-7
DownloadTélécharger
Actions
Vote :
ScreenshotAperçu
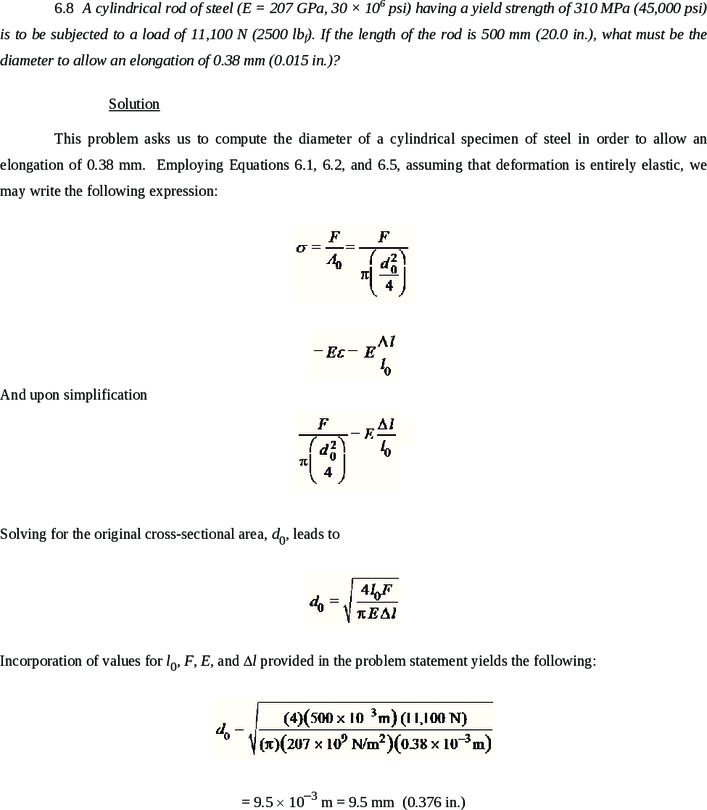
Informations
Catégorie :Category: mViewer GX Creator Lua TI-Nspire
Auteur Author: didierisaza
Type : Classeur 3.6
Page(s) : 20
Taille Size: 1.09 Mo MB
Mis en ligne Uploaded: 30/04/2015 - 09:09:34
Uploadeur Uploader: carl cox (Profil)
Téléchargements Downloads: 120
Visibilité Visibility: Archive publique
Shortlink : https://tipla.net/a205961
Type : Classeur 3.6
Page(s) : 20
Taille Size: 1.09 Mo MB
Mis en ligne Uploaded: 30/04/2015 - 09:09:34
Uploadeur Uploader: carl cox (Profil)
Téléchargements Downloads: 120
Visibilité Visibility: Archive publique
Shortlink : https://tipla.net/a205961
Description
6.8 A cylindrical rod of steel (E = 207 GPa, 30 × 106 psi) having a yield strength of 310 MPa (45,000 psi)
LVWREHVXEMHFWHGWRDORDGRI1OEf,IWKHOHQJWKRIWKHURGLVPPLQZKDWPXVWEHWKH
GLDPHWHUWRDOORZDQHORQJDWLRQRIPPLQ"
Solution
This problem asks us to compute the diameter of a cylindrical specimen of steel in order to allow an
elongation of 0.38 mm. Employing Equations 6.1, 6.2, and 6.5, assuming that deformation is entirely elastic, we
may write the following expression:
And upon simplification
Solving for the original cross-sectional area, d0, leads to
Incorporation of values for l0, F, E, and 'l provided in the problem statement yields the following:
3
= 9.5 u 10 m = 9.5 mm (0.376 in.)
6.15 A cylindrical specimen of steel having a diameter of 15.2 mm (0.60 in.) and length of 250 mm (10.0
LQLVGHIRUPHGHODVWLFDOOLQWHQVLRQZLWKDIRUFHRI1OEf). Using the data contained in Table 6.1,
GHWHUPLQHWKHIROORZLQJ
(a) The amounWEZKLFKWKLVVSHFLPHQZLOOHORQJDWHLQWKHGLUHFWLRQRIWKHDSSOLHGVWUHVV
(b) 7KHFKDQJHLQGLDPHWHURIWKHVSHFLPHQ:LOOWKHGLDPHWHULQFUHDVHRUGHFUHDVH"
Solution
(a) We are asked, in this portion of the problem, to determine the elongation of a cylindrical specimen of
steel. To solve this part of the problem requires that we use Equations 6.1, 6.2 and 6.5. Equation 6.5 reads as
follows:
Substitution the expression for V from Equation 6.1 and the expression for H from Equation 6.2 leads to
In this equation d0 is the original cross-sectional diameter. Now, solving for 'l yields
And incorporating values of F, l0, and d0, and realizing that E = 207 GPa (Table 6.1), leads to
(b) We are now called upon to determine the change in diameter, 'd. Using Equation 6.8 (the definition of
Poisson's ratio)
From Table 6.1, for steel, the value of Poisson's ratio, Q is 1RZVROYLQJWKHDERYHH[SUHVVLRQIRU࠾d yields
3 4
= –5.9 u 10 mm (–2.3 u 10 in.)
The diameter will decrease since 'd is negative.
6.21 A cylindrical metal specimen 15.0 mm (0.59 in.) in diameter and 150 mm (5.9 in.) long is to be
subjected to a tensile stress of 50 MPa (7250 psi); at this stress level, WKH UHVXOWLQJ GHIRUPDWLRQ ZLOO EH WRWDOO
elastic.
(a) If the elongation must be less tKDQ PP –3 LQ ZKLFK RI WKH PHWDOV LQ 7DEOH DUH
VXLWDEOHFDQGLGDWHV":K"
(b) If, in addition, the maximum permissible diameter decrease is 2.3 × 10–3 mm (9.1 × 10–5 LQZKHQWKH
WHQVLOHVWUHVVRI03DLVDSSOLHGZKLFKRIWKHPHWDOVWKDWVDWLVIWKHFULWHULRQLQSDUWDDUHVXLWDEOHFDQGLGDWHV"
:K"
Solution
(a) This part of the problem asks that we ascertain which of the metals in Table 6.1 experience an
elongation of less than 0.072 mm when subjected to a tensile stress of 50 MPa. The maximum strain that may be
sustained, (using Equation 6.2) is just
Since the stress level is given (50 MPa), using Equation 6.5 it is possible to compute the minimum modulus of
elasticity that is required to yield this minimum strain. Hence
Which means that those metals with moduli of elasticity greater than this value are acceptable candidates--namely,
Cu, Ni, steel, Ti and W.
(b) This portion of the problem further stipulates that the maximum permissible diameter decrease is 2.3 u
mm when the tensile stress of 50 MPa is applied. This translates into a maximum lateral strain Hx(max) as
-3
10
But, since the specimen contracts in this lateral direction, and we are concerned that this strain be less than 1.53 u
10-4, then the criterion for this part of the problem may be stipulated as
Now, Poisson’s ratio is defined by Equation 6.8 as
For each of the metal alloys let us consider a possible lateral strain, . Furthermore, since the deformation is
elastic, then, from Equation 6.5, the longitudinal strain, Hz is equal to
Substituting these expressions for Hx and Hz into the definition of Poisson’s ratio we have
which leads to the following:
Using values for Q and E found in Table 6.1 for the six metal alloys that satisfy the criterion for part (a), and for V =
50 MPa, we are able to compute a for each of Cu, Ni, steel, Ti and W as follows:
Thus, copper and titanium alloys will experience a negative transverse strain greater than 1.53 u 104. This means
that the following alloys satisfy the criteria for both parts (a) and (b) of this problem: nickel, steel, and tungsten.
6.22 A cylindrical metal specimen 10.7000 mm in diameter and 95.000 mm long is to be subjected to a
WHQVLOHIRUFHRI1DWWKLVIRUFHOHYHO, WKHUHVXOWLQJGHIRUPDWLRQZLOOEe totally elastic.
(a) ,I WKH ILQDO OHQJWK PXVW EH OHVV WKDQ PP ZKLFK RI WKH PHWDOV LQ 7DEOH DUH VXLWDEOH
FDQGLGDWHV":K"
(b) If, in addition, the diameter must be no greater WKDQ PP ZKLOH WKH WHQVLOH IRUFH RI 1 LV
DSSOLHGZKLFKRIWKHPHWDOVWKDWVDWLVIWKHFULWHULRQLQSDUWDDUHVXLWDEOHFDQGLGDWHV":K"
Solution
(a) This part of the problem asks that we ascertain which of the metals in Table 6.1 experience an increase
in length from 95.000 mm (l0) to 95.040 mm (li) when subjected to a tensile force of 6300 N. We may make this
determination by computing the minimum modulus of elasticity required using data given in the problem statement;
those metals having values greater than this minimum satisfy the criterion. Modulus of elasticity is determined
using Equation 6.5 (V = HE), which requires that we first compute values for the stress and strain.
The maximum strain that may be sustained, (using Equation 6.2) is just
The maximum stress level is computed using Equation 6.1; original cross-sectional area (A0) may be determined
from original specimen diameter (d0 = 10.7000 mm). Thus, the stress is equal to
We now calculate the minimum modulus of elasticity incorporating these stress and strain values into Equation 6.5.
Hence
Which means that those metals with moduli of elasticity greater than this value are acceptable candidates--namely,
Ni, steel, and W.
(b) For this part of the problem it is necessary to ascertain which of nickel, steel, and tungsten will have
diameters of no greater than 10.698 while the 6300 N force is being applied. This determination can be made by
computing the maximum allowable Poisson's ratio (Equation 6.8) from the ratio of transverse and longitudinal
strains (Hx and Hz, respectively). The strain calculated in part (a) is a longitudinal strain—i.e.,
Transverse strain (Hx)is computed using the transverse analog of Equation 6.2—i.e.,
In this equation di is the diameter while the stress is being applied—i.e., 10.698 mm. Thus
We now compute Poisson's ratio using Equation 6.8 as follows:
This result means that for deformed diameters to be less than 10.698 mm, the value of Poisson's ratio must be less
than 0.444—therefore, all of nickel (Q = 0.31), steel (Q = 0.30), and tungsten (Q = 0.28) are candidates.
Therefore, of these four alloys, only brass and steel satisfy the stipulated criteria.
Tensile Properties
6.26 )LJXUHVKRZVWKHWHQVLOHHQJLQHHULQJVWUHVV–strain behavior for a steel alloy.
D:KDWLVWKHPRGXOXVRIHODVWLFLW"
(b) What is the SURSRUWLRQDOOLPLW"
F:KDWLVWKHLHOGVWUHQJWKDWDVWUDLQRIIVHWRI"
G:KDWLVWKHWHQVLOHVWUHQJWK"
Solution
(a) Shown below is the inset of Figure 6.22.
The elastic modulus is just the slope of the initial linear portion of the curve; or, from Equation 6.10
Inasmuch as the linear segment passes through the origin, let us take both V and H to be zero. If we arbitrarily take
H = 0.005, as noted in the above plot, V = 1050 MPa. Using these stress and strain values we calculate the elastic
modulus as follows:
The value given in Table 6.1 is 207 GPa.
(b) The proportional limit is the stress level at which linearity of the stress-strain curve ends, which is
approximately 1370 MPa (200,000 psi).
(c) As noted in the plot below, the 0.002 strain offset line intersects the stress-strain curve at approximately
1600 MPa (232,000 psi).
(d) The tensile strength (the maximum on the curve) is approximately 1950 MPa (283,000 psi), as noted in
the following plot.
6.30 A FOLQGULFDOVSHFLPHQRIVWDLQOHVVVWHHOKDYLQJDGLDPHWHURIPPLQDQGDJDXJHOHQJWK
RIPPLQLVSXOOHGLQWHQVLRQ8VHWKHORDG–HORQJDWLRQFKDUDFWHULVWLFVVKRZQLQWKHIROORZLQJWDEOH
to complete parts (a) through (f).
Load Length
N lbf mm in.
0 0 2.000
12,700 2.001
25,400 5,710 2.002
2.003
11,400 50.902 2.004
76,200 17,100 50.952 2.006
20,000 51.003
92,700 51.054 2.010
102,500 23,000 2.015
24,200 2.020
119,400 51.562 2.030
2.040
149,700 33,650
159,000 35,750 2.120
160,400 36,000 54.356 2.140
159,500 2.160
151,500 34,050 2.200
124,700 56.642 2.230
Fracture
(a) Plot the data as engineering stress versus engineering strain.
(b) Compute the modulus of elasticity.
(c) Determine the yield strength at a strain offset of 0.002.
(d) Determine the tensile strength of this alloy.
(e) What is WKHDSSUR[LPDWHGXFWLOLWLQSHUFHQWHORQJDWLRQ"
(f) Compute the modulus of resilience.
Solution
This problem calls for us to make a stress-strain plot for stainless steel, given its tensile load-length data,
and then to determine some of its mechanical characteristics.
(a) The data are plotted below on two plots: the first corresponds to the entire stress-strain curve, while for
the second, the curve extends to just beyond the elastic region of deformation.
(b) The elastic modulus is the slope in the linear elastic region (Equation 6.10)—i.e.,
Because the stress-strain curve passes through the origin, to simplify the computation let us take both V and H to be
zero. If we select V = 400 MPa, its corresponding strain on the plot H is about 0.002. Thus the elastic modulus is
equal to
(c) For the yield strength, the 0.002 strain offset line is drawn dashed in the lower plot. It intersects the
stress-strain curve at approximately 750 MPa (112,000 psi ).
(d) The tensile strength is approximately 1250 MPa (180,000 psi), corresponding to the maximum stress
on the complete stress-strain plot.
(e) Ductility, in percent elongation, is just the plastic strain at fracture, multiplied by one-hundred. The
total fracture strain at fracture is 0.115; subtracting out the elastic strain (which is about 0.003) leaves a plastic strain
of 0.112. Thus, the ductility is about 11.2%EL.
(f) From Equation 6.14, the modulus of resilience is just
which, using values of Vy and E computed above, (750 MPa = 750 u 106 N/m2 and 200 GPa = 200 u 109 N/m2,
respectively) give a modulus of resilience of
Slip Systems
7.5 (a) Define a slip system.
(b) Do all metals have the same slip system? Why or why not?
Answer
(a) A slip system is a crystallographic plane, and, within that plane, a direction along which dislocation
motion (or slip) occurs.
(b) All metals do not have the same slip system. The reason for this is that for most metals, the slip system
will consist of the most densely packed crystallographic plane, and within that plane the most closely packed
direction. This plane and direction will vary from crystal structure to crystal structure.
Slip in Single Crystals
7.11 Sometimes in Equation 7.2 is termed the Schmid factor. Determine the magnitude of the
Schmid factor for an FCC single crystal oriented with its [120] direction parallel to the loading axis.
Solution
We are asked to compute the Schmid factor for an FCC crystal oriented with its [120] direction parallel to
the loading axis. With this scheme, slip may occur on the (111) plane and in the direction as noted in the
figure below.
The angle between the [120] and directions, O, may be determined using Equation 7.6
where (for [120]) u1 = 1, v1 = 2, w1 = 0, and (for ) u2 = 0, v2 = 1, w2 = 1. Therefore, O is equal to
Now, the angle I is equal to the angle between the normal to the (111) plane (which is the [111] direction), and the
[120] direction. Again from Equation 7.6, and for u1 = 1, v1 = 1, w1 = 1, and u2 = 1, v2 = 2, and w2 = 0, we have
Therefore, the Schmid factor is equal to
7.12 Consider a metal single crystal oriented such that the normal to the slip plane and the slip direction
are at angles of 60° and 35°, respectively, with the tensile axis. If the critical resolved shear stress is 6.2 MPa (900
psi), will an applied stress of 12 MPa (1750 psi) cause the single crystal to yield? If not, what stress will be
necessary?
Solution
This problem calls for us to determine whether or not a metal single crystal having a specific orientation
and of given critical resolved shear stress will yield. We are given that I = 60q, O = 35q, and that the values of the
critical resolved shear stress and applied tensile stress are 6.2 MPa (900 psi) and 12 MPa (1750 psi), respectively.
From Equation 7.2
Since the resolved shear stress (4.91 MPa) is less that the critical resolved shear stress (6.2 MPa), the single crystal
will not yield.
However, from Equation 7.4, the stress at which yielding occurs is
7.18 Consider a single crystal of some hypothetical metal that has the FCC crystal structure and is
oriented such that a tensile stress is applied along a direction. If slip occurs on a (111) plane and in a
direction, and the crystal yields at a stress of 5.12 MPa compute the critical resolved shear stress.
Solution
To solve this problem we use Equation 7.4; however it is first necessary to determine the values of I and O.
These determinations are possible using Equation 7.6. Now, O is the angle between and directions.
Therefore, relative to Equation 7.6 let us take u1 = 1, v1 = 1, and w1 = 2, as well as u2 = 0, v2 = 1, and w2 = 1. This
leads to
Now for the determination of I, the normal to the (111) slip plane is the [111] direction. Again using Equation 7.6,
where we now take u1 = 1, v1 = 1, w1 = 2 (for ), and u2 = 1, v2 = 1, w2 = 1 (for [111]). Thus,
It is now possible to compute the critical resolved shear stress (using Equation 7.4) as
Deformation by Twinning
7.20 List four major differences between deformation by twinning and deformation by slip relative to
mechanism, conditions of occurrence, and final result.
Solution
Four major differences between deformation by twinning and deformation by slip are as follows: (1) with
slip deformation there is no crystallographic reorientation, whereas with twinning there is a reorientation; (2) for
slip, the atomic displacements occur in atomic spacing multiples, whereas for twinning, these displacements may be
other than by atomic spacing multiples; (3) slip occurs in metals having many slip systems, whereas twinning
occurs in metals having relatively few slip systems; and (4) normally slip results in relatively large deformations,
whereas only small deformations result for twinning.
7.31 A cylindrical specimen of cold-worked copper has a ductility (%EL) of 15%. If its cold-worked radius
is 6.4 mm (0.25 in.), what was its radius before deformation?
Solution
This problem calls for us to calculate the precold-worked radius of a cylindrical specimen of copper that
has a cold-worked ductility of 15%EL. From Figure 7.19c, copper that has a ductility of 15%EL will have
experienced a deformation of about 20%CW. For a cylindrical specimen, Equation 7.8 becomes
Since rd = 6.4 mm (0.25 in.), solving for r0 yields
LVWREHVXEMHFWHGWRDORDGRI1OEf,IWKHOHQJWKRIWKHURGLVPPLQZKDWPXVWEHWKH
GLDPHWHUWRDOORZDQHORQJDWLRQRIPPLQ"
Solution
This problem asks us to compute the diameter of a cylindrical specimen of steel in order to allow an
elongation of 0.38 mm. Employing Equations 6.1, 6.2, and 6.5, assuming that deformation is entirely elastic, we
may write the following expression:
And upon simplification
Solving for the original cross-sectional area, d0, leads to
Incorporation of values for l0, F, E, and 'l provided in the problem statement yields the following:
3
= 9.5 u 10 m = 9.5 mm (0.376 in.)
6.15 A cylindrical specimen of steel having a diameter of 15.2 mm (0.60 in.) and length of 250 mm (10.0
LQLVGHIRUPHGHODVWLFDOOLQWHQVLRQZLWKDIRUFHRI1OEf). Using the data contained in Table 6.1,
GHWHUPLQHWKHIROORZLQJ
(a) The amounWEZKLFKWKLVVSHFLPHQZLOOHORQJDWHLQWKHGLUHFWLRQRIWKHDSSOLHGVWUHVV
(b) 7KHFKDQJHLQGLDPHWHURIWKHVSHFLPHQ:LOOWKHGLDPHWHULQFUHDVHRUGHFUHDVH"
Solution
(a) We are asked, in this portion of the problem, to determine the elongation of a cylindrical specimen of
steel. To solve this part of the problem requires that we use Equations 6.1, 6.2 and 6.5. Equation 6.5 reads as
follows:
Substitution the expression for V from Equation 6.1 and the expression for H from Equation 6.2 leads to
In this equation d0 is the original cross-sectional diameter. Now, solving for 'l yields
And incorporating values of F, l0, and d0, and realizing that E = 207 GPa (Table 6.1), leads to
(b) We are now called upon to determine the change in diameter, 'd. Using Equation 6.8 (the definition of
Poisson's ratio)
From Table 6.1, for steel, the value of Poisson's ratio, Q is 1RZVROYLQJWKHDERYHH[SUHVVLRQIRU࠾d yields
3 4
= –5.9 u 10 mm (–2.3 u 10 in.)
The diameter will decrease since 'd is negative.
6.21 A cylindrical metal specimen 15.0 mm (0.59 in.) in diameter and 150 mm (5.9 in.) long is to be
subjected to a tensile stress of 50 MPa (7250 psi); at this stress level, WKH UHVXOWLQJ GHIRUPDWLRQ ZLOO EH WRWDOO
elastic.
(a) If the elongation must be less tKDQ PP –3 LQ ZKLFK RI WKH PHWDOV LQ 7DEOH DUH
VXLWDEOHFDQGLGDWHV":K"
(b) If, in addition, the maximum permissible diameter decrease is 2.3 × 10–3 mm (9.1 × 10–5 LQZKHQWKH
WHQVLOHVWUHVVRI03DLVDSSOLHGZKLFKRIWKHPHWDOVWKDWVDWLVIWKHFULWHULRQLQSDUWDDUHVXLWDEOHFDQGLGDWHV"
:K"
Solution
(a) This part of the problem asks that we ascertain which of the metals in Table 6.1 experience an
elongation of less than 0.072 mm when subjected to a tensile stress of 50 MPa. The maximum strain that may be
sustained, (using Equation 6.2) is just
Since the stress level is given (50 MPa), using Equation 6.5 it is possible to compute the minimum modulus of
elasticity that is required to yield this minimum strain. Hence
Which means that those metals with moduli of elasticity greater than this value are acceptable candidates--namely,
Cu, Ni, steel, Ti and W.
(b) This portion of the problem further stipulates that the maximum permissible diameter decrease is 2.3 u
mm when the tensile stress of 50 MPa is applied. This translates into a maximum lateral strain Hx(max) as
-3
10
But, since the specimen contracts in this lateral direction, and we are concerned that this strain be less than 1.53 u
10-4, then the criterion for this part of the problem may be stipulated as
Now, Poisson’s ratio is defined by Equation 6.8 as
For each of the metal alloys let us consider a possible lateral strain, . Furthermore, since the deformation is
elastic, then, from Equation 6.5, the longitudinal strain, Hz is equal to
Substituting these expressions for Hx and Hz into the definition of Poisson’s ratio we have
which leads to the following:
Using values for Q and E found in Table 6.1 for the six metal alloys that satisfy the criterion for part (a), and for V =
50 MPa, we are able to compute a for each of Cu, Ni, steel, Ti and W as follows:
Thus, copper and titanium alloys will experience a negative transverse strain greater than 1.53 u 104. This means
that the following alloys satisfy the criteria for both parts (a) and (b) of this problem: nickel, steel, and tungsten.
6.22 A cylindrical metal specimen 10.7000 mm in diameter and 95.000 mm long is to be subjected to a
WHQVLOHIRUFHRI1DWWKLVIRUFHOHYHO, WKHUHVXOWLQJGHIRUPDWLRQZLOOEe totally elastic.
(a) ,I WKH ILQDO OHQJWK PXVW EH OHVV WKDQ PP ZKLFK RI WKH PHWDOV LQ 7DEOH DUH VXLWDEOH
FDQGLGDWHV":K"
(b) If, in addition, the diameter must be no greater WKDQ PP ZKLOH WKH WHQVLOH IRUFH RI 1 LV
DSSOLHGZKLFKRIWKHPHWDOVWKDWVDWLVIWKHFULWHULRQLQSDUWDDUHVXLWDEOHFDQGLGDWHV":K"
Solution
(a) This part of the problem asks that we ascertain which of the metals in Table 6.1 experience an increase
in length from 95.000 mm (l0) to 95.040 mm (li) when subjected to a tensile force of 6300 N. We may make this
determination by computing the minimum modulus of elasticity required using data given in the problem statement;
those metals having values greater than this minimum satisfy the criterion. Modulus of elasticity is determined
using Equation 6.5 (V = HE), which requires that we first compute values for the stress and strain.
The maximum strain that may be sustained, (using Equation 6.2) is just
The maximum stress level is computed using Equation 6.1; original cross-sectional area (A0) may be determined
from original specimen diameter (d0 = 10.7000 mm). Thus, the stress is equal to
We now calculate the minimum modulus of elasticity incorporating these stress and strain values into Equation 6.5.
Hence
Which means that those metals with moduli of elasticity greater than this value are acceptable candidates--namely,
Ni, steel, and W.
(b) For this part of the problem it is necessary to ascertain which of nickel, steel, and tungsten will have
diameters of no greater than 10.698 while the 6300 N force is being applied. This determination can be made by
computing the maximum allowable Poisson's ratio (Equation 6.8) from the ratio of transverse and longitudinal
strains (Hx and Hz, respectively). The strain calculated in part (a) is a longitudinal strain—i.e.,
Transverse strain (Hx)is computed using the transverse analog of Equation 6.2—i.e.,
In this equation di is the diameter while the stress is being applied—i.e., 10.698 mm. Thus
We now compute Poisson's ratio using Equation 6.8 as follows:
This result means that for deformed diameters to be less than 10.698 mm, the value of Poisson's ratio must be less
than 0.444—therefore, all of nickel (Q = 0.31), steel (Q = 0.30), and tungsten (Q = 0.28) are candidates.
Therefore, of these four alloys, only brass and steel satisfy the stipulated criteria.
Tensile Properties
6.26 )LJXUHVKRZVWKHWHQVLOHHQJLQHHULQJVWUHVV–strain behavior for a steel alloy.
D:KDWLVWKHPRGXOXVRIHODVWLFLW"
(b) What is the SURSRUWLRQDOOLPLW"
F:KDWLVWKHLHOGVWUHQJWKDWDVWUDLQRIIVHWRI"
G:KDWLVWKHWHQVLOHVWUHQJWK"
Solution
(a) Shown below is the inset of Figure 6.22.
The elastic modulus is just the slope of the initial linear portion of the curve; or, from Equation 6.10
Inasmuch as the linear segment passes through the origin, let us take both V and H to be zero. If we arbitrarily take
H = 0.005, as noted in the above plot, V = 1050 MPa. Using these stress and strain values we calculate the elastic
modulus as follows:
The value given in Table 6.1 is 207 GPa.
(b) The proportional limit is the stress level at which linearity of the stress-strain curve ends, which is
approximately 1370 MPa (200,000 psi).
(c) As noted in the plot below, the 0.002 strain offset line intersects the stress-strain curve at approximately
1600 MPa (232,000 psi).
(d) The tensile strength (the maximum on the curve) is approximately 1950 MPa (283,000 psi), as noted in
the following plot.
6.30 A FOLQGULFDOVSHFLPHQRIVWDLQOHVVVWHHOKDYLQJDGLDPHWHURIPPLQDQGDJDXJHOHQJWK
RIPPLQLVSXOOHGLQWHQVLRQ8VHWKHORDG–HORQJDWLRQFKDUDFWHULVWLFVVKRZQLQWKHIROORZLQJWDEOH
to complete parts (a) through (f).
Load Length
N lbf mm in.
0 0 2.000
12,700 2.001
25,400 5,710 2.002
2.003
11,400 50.902 2.004
76,200 17,100 50.952 2.006
20,000 51.003
92,700 51.054 2.010
102,500 23,000 2.015
24,200 2.020
119,400 51.562 2.030
2.040
149,700 33,650
159,000 35,750 2.120
160,400 36,000 54.356 2.140
159,500 2.160
151,500 34,050 2.200
124,700 56.642 2.230
Fracture
(a) Plot the data as engineering stress versus engineering strain.
(b) Compute the modulus of elasticity.
(c) Determine the yield strength at a strain offset of 0.002.
(d) Determine the tensile strength of this alloy.
(e) What is WKHDSSUR[LPDWHGXFWLOLWLQSHUFHQWHORQJDWLRQ"
(f) Compute the modulus of resilience.
Solution
This problem calls for us to make a stress-strain plot for stainless steel, given its tensile load-length data,
and then to determine some of its mechanical characteristics.
(a) The data are plotted below on two plots: the first corresponds to the entire stress-strain curve, while for
the second, the curve extends to just beyond the elastic region of deformation.
(b) The elastic modulus is the slope in the linear elastic region (Equation 6.10)—i.e.,
Because the stress-strain curve passes through the origin, to simplify the computation let us take both V and H to be
zero. If we select V = 400 MPa, its corresponding strain on the plot H is about 0.002. Thus the elastic modulus is
equal to
(c) For the yield strength, the 0.002 strain offset line is drawn dashed in the lower plot. It intersects the
stress-strain curve at approximately 750 MPa (112,000 psi ).
(d) The tensile strength is approximately 1250 MPa (180,000 psi), corresponding to the maximum stress
on the complete stress-strain plot.
(e) Ductility, in percent elongation, is just the plastic strain at fracture, multiplied by one-hundred. The
total fracture strain at fracture is 0.115; subtracting out the elastic strain (which is about 0.003) leaves a plastic strain
of 0.112. Thus, the ductility is about 11.2%EL.
(f) From Equation 6.14, the modulus of resilience is just
which, using values of Vy and E computed above, (750 MPa = 750 u 106 N/m2 and 200 GPa = 200 u 109 N/m2,
respectively) give a modulus of resilience of
Slip Systems
7.5 (a) Define a slip system.
(b) Do all metals have the same slip system? Why or why not?
Answer
(a) A slip system is a crystallographic plane, and, within that plane, a direction along which dislocation
motion (or slip) occurs.
(b) All metals do not have the same slip system. The reason for this is that for most metals, the slip system
will consist of the most densely packed crystallographic plane, and within that plane the most closely packed
direction. This plane and direction will vary from crystal structure to crystal structure.
Slip in Single Crystals
7.11 Sometimes in Equation 7.2 is termed the Schmid factor. Determine the magnitude of the
Schmid factor for an FCC single crystal oriented with its [120] direction parallel to the loading axis.
Solution
We are asked to compute the Schmid factor for an FCC crystal oriented with its [120] direction parallel to
the loading axis. With this scheme, slip may occur on the (111) plane and in the direction as noted in the
figure below.
The angle between the [120] and directions, O, may be determined using Equation 7.6
where (for [120]) u1 = 1, v1 = 2, w1 = 0, and (for ) u2 = 0, v2 = 1, w2 = 1. Therefore, O is equal to
Now, the angle I is equal to the angle between the normal to the (111) plane (which is the [111] direction), and the
[120] direction. Again from Equation 7.6, and for u1 = 1, v1 = 1, w1 = 1, and u2 = 1, v2 = 2, and w2 = 0, we have
Therefore, the Schmid factor is equal to
7.12 Consider a metal single crystal oriented such that the normal to the slip plane and the slip direction
are at angles of 60° and 35°, respectively, with the tensile axis. If the critical resolved shear stress is 6.2 MPa (900
psi), will an applied stress of 12 MPa (1750 psi) cause the single crystal to yield? If not, what stress will be
necessary?
Solution
This problem calls for us to determine whether or not a metal single crystal having a specific orientation
and of given critical resolved shear stress will yield. We are given that I = 60q, O = 35q, and that the values of the
critical resolved shear stress and applied tensile stress are 6.2 MPa (900 psi) and 12 MPa (1750 psi), respectively.
From Equation 7.2
Since the resolved shear stress (4.91 MPa) is less that the critical resolved shear stress (6.2 MPa), the single crystal
will not yield.
However, from Equation 7.4, the stress at which yielding occurs is
7.18 Consider a single crystal of some hypothetical metal that has the FCC crystal structure and is
oriented such that a tensile stress is applied along a direction. If slip occurs on a (111) plane and in a
direction, and the crystal yields at a stress of 5.12 MPa compute the critical resolved shear stress.
Solution
To solve this problem we use Equation 7.4; however it is first necessary to determine the values of I and O.
These determinations are possible using Equation 7.6. Now, O is the angle between and directions.
Therefore, relative to Equation 7.6 let us take u1 = 1, v1 = 1, and w1 = 2, as well as u2 = 0, v2 = 1, and w2 = 1. This
leads to
Now for the determination of I, the normal to the (111) slip plane is the [111] direction. Again using Equation 7.6,
where we now take u1 = 1, v1 = 1, w1 = 2 (for ), and u2 = 1, v2 = 1, w2 = 1 (for [111]). Thus,
It is now possible to compute the critical resolved shear stress (using Equation 7.4) as
Deformation by Twinning
7.20 List four major differences between deformation by twinning and deformation by slip relative to
mechanism, conditions of occurrence, and final result.
Solution
Four major differences between deformation by twinning and deformation by slip are as follows: (1) with
slip deformation there is no crystallographic reorientation, whereas with twinning there is a reorientation; (2) for
slip, the atomic displacements occur in atomic spacing multiples, whereas for twinning, these displacements may be
other than by atomic spacing multiples; (3) slip occurs in metals having many slip systems, whereas twinning
occurs in metals having relatively few slip systems; and (4) normally slip results in relatively large deformations,
whereas only small deformations result for twinning.
7.31 A cylindrical specimen of cold-worked copper has a ductility (%EL) of 15%. If its cold-worked radius
is 6.4 mm (0.25 in.), what was its radius before deformation?
Solution
This problem calls for us to calculate the precold-worked radius of a cylindrical specimen of copper that
has a cold-worked ductility of 15%EL. From Figure 7.19c, copper that has a ductility of 15%EL will have
experienced a deformation of about 20%CW. For a cylindrical specimen, Equation 7.8 becomes
Since rd = 6.4 mm (0.25 in.), solving for r0 yields